Es ist vollbracht; die letzten großen Teile der Hauptfahrwerksfelge sind entstanden. Der Reihe nach:
Zunächst geprüft, ob das Vorhaben zumindest grob machbar erscheint. Das ist der Fall, da auf der BF20 mit einem, sehr präzisen, geliehenen 125er Drehtisch (vielen Dank, Kongo!) gerade noch genug Platz für die Bearbeitung bleibt (5 mm nach vorne und immerhin noch 2 mm nach oben – das ist geradezu luxuriös, wenn man vergleicht, wie wenig Platz beim Drehen zum Schlitten existiert 😉
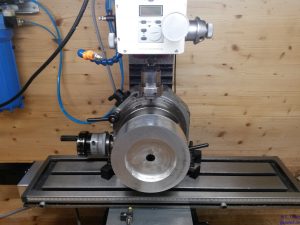
Passprobe auf der BF20.
Kurze Zeit und 3 Säcke AW7075-Späne später fällt dann der erste Drehling von der CNC-Drehbank, bei dem die N7-Passung für das spätere Kugellagergehäuse auch wirklich stimmt (3x Ausschuss – besonders ärgerlich, da die Bearbeitungszeit auf meiner 0,8 kW „starken“ Drehbank durch die kleine Zustellung doch recht lang ist!):
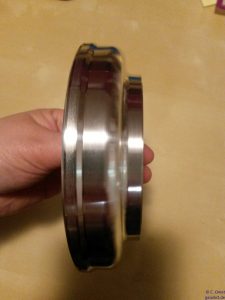
Bremsenseite Hauptfahrwerksfelge, Drehling.
Schließlich die Innenseite auf der BF20 freigefräst und mit Kernbohrung für das M6-Gewinde versehen:
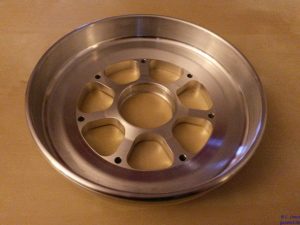
Bremsenseite Hauptfahrwerksfelge, freigefräst.
… und zu guter Letzt die Ausschnitte für die Befestigung der Behringer-Bremsscheibe (Zukaufteil!) mit radialer Bearbeitungsrichtung gefräst, gefast, gebohrt und schließlich mit M6- und M2,5-Gewinden versehen. Der erste Schritt ist dabei besonders peinsam, denn das Felgenteil hat die akustischen Eigenschaften einer Glocke und schwingt beim Fräsen sofort auf. Also die Schwingung von außen bedämpft – und zwar mit der nicht zur Nachahmung empfohlenen Vorgehensweise per Hand…
Wenn ich sowas nochmal machen sollte, gibt’s eine separate Spannvorrichtung (und eine größere Fräse, denn dafür ist auf meiner BF20 schlicht und ergreifend kein Platz mehr). Auf dem Bild links unten ist die Bremsscheibe zur Verdeutlichung schon mal eingelegt.
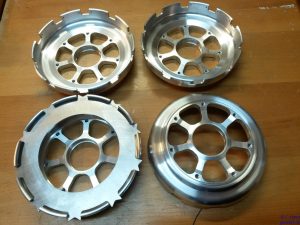
Bremsenseite Hauptfahrwerksfelge fertig.
Das war das bisher mit Abstand komplizierteste Einzelteil, was ich in einer Kleinserie jemals hergestellt habe (wohl dem, der ein 5-Achs-Bearbeitungszentrum mit automatischem Werkzeugwechsler sein eigen nennt)!
Fehlen nur noch die kleinen V2A-Blechbiegeteile zur schwimmenden Lagerung der Bremsscheibe auf der Felge. Das V2A hat eine fast 10-fach geringere Wärmeleitfähigkeit als AW7075 und wird benötigt, damit beim Bremsen die Felge nicht weich wird…
Bilder vom Zusammenbau folgen (schon probiert, passt alles) 😀