Die Holme sind 3,63 m lang, was planmäßig fast die ganze Länge meiner Werkbank in Beschlag nimmt. Die Holmgurte bestehen aus pultrudierten CFK-Leisten (Kaufteil!), welche in ein Sandwich aus Oregon Pine- und Buchenleisten „verpackt“ werden. Ich habe mich nach Analyse des FEM-Modells dazu entschieden, die CFK-Leisten 6 mm weiter nach außen zu legen als ursprünglich vorgesehen. Damit nehmen sie die Zug- und Druckkräfte besser auf. Die dort vorgesehenen Holzleisten habe ich nach innen verlegt, so dass Gesamtstärke und -Gewicht gleich bleibt.
Zunächst eine schön glatte und ausnivellierte Unterlage aus Paneelen hergestellt. Darauf mit der extralangen Richtlatte zwei Alu-Rechteckleisten ausgerichtet und diese im Soll-Abstand von 134 mm auf die Paneele geschraubt. Darauf eine Lage Paketklebeband zum Trennen.
Dann alle Leisten abgelängt, (teilweise konisch) abgehobelt und jeweils ein Pärchen mit angedicktem Harz verklebt:
![]() | ![]() |
Nach dem Verschleifen sieht das Ganze so aus (die Perspektive verfälscht die Geometrie; der sich im Rumpf befindliche Teil geht bis zu den Buchenklötzen und ist ca. 1 m lang):
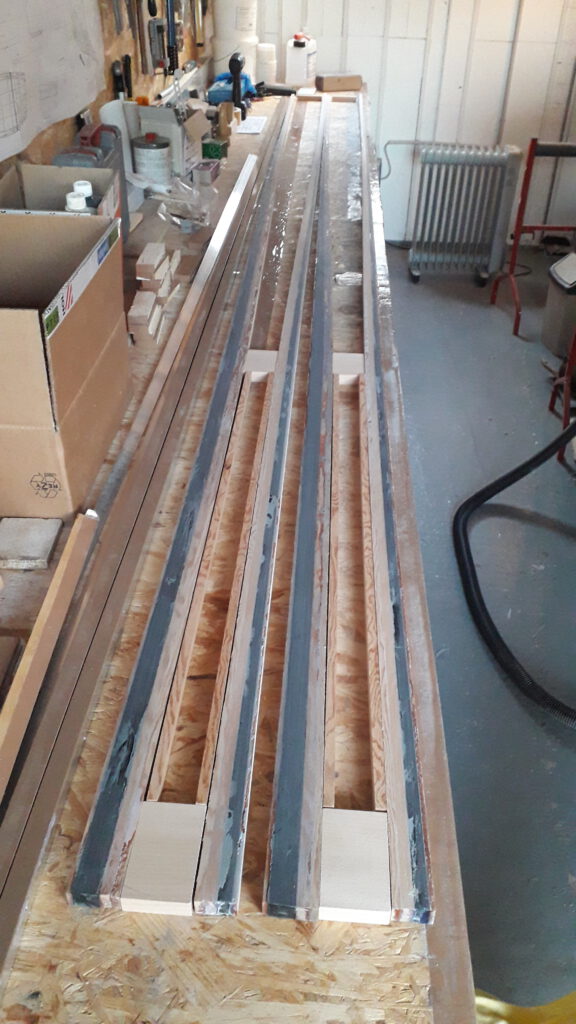
Jetzt warten die Einzelteile noch auf die Füllung mit Rohazell und den weiteren Zusammenbau. Danach muss erst der Prüfer einen Blick drauf werfen, bevor sie mit 45°-Bidiagonalgewebe umwickelt werden.
Nachtrag (07/22): Mittlerweile sind die Holme gefüllt, verklebt, abgeschliffen und vom Prüfer abgenommen. Sie harren noch der Umwicklung mit dem 45°-Bidiagonalgewebe. Dafür braucht’s noch etwas Platz auf dem Arbeitstisch und Vorbereitung der ganzen Vakuumtechnik.