… lange hat sich im Bautagebuch nichts getan, doch jetzt geht es wieder weiter. Treibende Quelle der Verzögerung: Die Drehbank (Bernardo Profi 550 WQ) soll demnächst dazu verwendet werden, Achsen und Felgen herzustellen. Einzelmaßnahmen hierzu:
- Schrittmotoren an X- und Z-Achse angebaut,
- die Elektronik (besser: Elektrik) komplett neu verkabelt,
- den 400 V-Motor an einen Frequenzumrichter (FU) angeschlossen,
- die Spindel mit einer Lichtschranke nebst Encoder ausgestattet,
- eine Steuerung mit Leadshine-Endstufen und 0-10 V-Ausgang (FU-Steuerung) aufgebaut,
- den kompletten Schlosskasten nebst Zahnstangen und Vorschubgetriebe ausgebaut und
- schließlich beide Achsen mit Kugelumlaufspindeln nebst neuen Fest- und Loslagern versehen. Dazu musste
- der X-Schlitten zur Aufnahme der Kugelumlaufmutter ausgefräst,
- die Kugelumlaufmutter abgefräst (wozu habe ich denn eine Fräse… – da gehärtet, ging es nur mit VHM-Fräser),
- die Schlittenführungen neu geschabt (wohl eher: das erste Mal geschabt, vorher war da wohl einer mit der Flex dran),
- neue Halter für die Teleskopabdeckungen gefertigt und
- neue Aufnahmebohrungen für die Lager am Gussbett (frei Hand) hergestellt werden.
Einige Bilder vom Umbau:
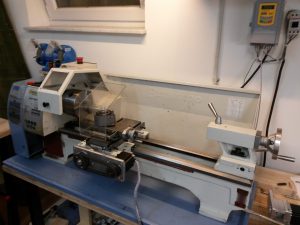
Bernardo-Zwischenzustand.
Einige Bauteile für die Z-Achse (alles aus AW 7075 hergestellt, das war gerade günstig verfügbar):
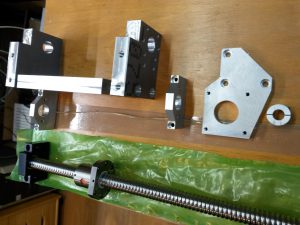
Bauteile für die Z-Achse.
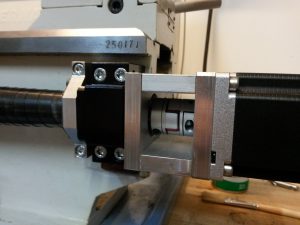
Detail der Z-Achse.
Fertiger Umbau:
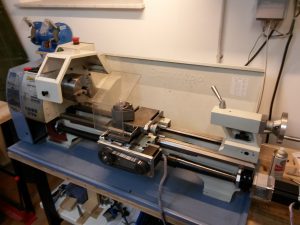
Bernardo-Upgrade!
Lohn der Mühe: Die Z-Achse läuft mit 4 m/min, die X-Achse mit 2 m/min. Das Umkehrspiel der Achsen, welches vorher (X/Z) ca. 0,4 mm/0,6 mm betrug, ist praktisch vollständig weg (bis auf 2-3/100 mm). Kein Umlegen des Keilriemens mehr, kein Wechseln der Zahnräder mehr, kein nerviges Getrieberattern mehr… Erste Teststücke nebst Gewinde sind auch schon abgefallen, da muss man echt zusehen, dass man die Späne schnell wegbekommt.
Damit kann das Fahrwerk endlich in Angriff genommen werden! 🙂
Nebenbei habe ich die komplette Werkstatt umgeräumt, festgestellt, dass der Wasserschaden vom Sommer doch etwas ausgedehnter war. Weiterhin die Fräse auch gleich auf die neue Steuerung umgebaut, an den FU angeschlossen und meinen 2D-Kantentaster elektronifiziert und ebenfalls mit der Steuerung verbunden. Nie mehr Drehzahl von Hand einstellen (bzw. vergessen) und Nullpunkte suchen…