Mal wieder so eine langwierige Ausrichtungsangelegenheit: Die Fahrwerksschwinge…
Fahrwerksschwinge zwischen C3 und C4 eingefädelt, Halter auf dieser verschraubt und gemerkt, dass meine Konstruktion einige (behebbare) Schwächen aufweist – wird später korrigiert.
Dann die Stahlbolzen passend abgelängt und dabei festgestellt, dass bei meiner Gazaile aus geometrischen Gründen der linke Flügelholm vor den rechten kommen muss. Die Schwinge mit Wasserwaage und mehrfacherer Referenznahme zum Rumpfholm und -Boden ausgerichtet. Danach Lochpositionen an den Spanten angezeichnet und mit 90°-Winkelvorsatz gebohrt. Probesitz:
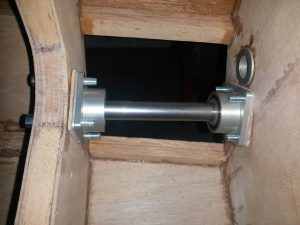
Fahrwerkshalter rechts.
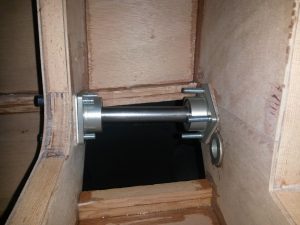
Fahrwerkshalter links.
Der Spant C3 muss von der schlecht zugänglichen Rückseite flach angesenkt werden, damit die Aluhülsen eingepasst werden können (mit selbstgeschliffenem Spezial-Forstnerbohrer). Scheint zu passen:
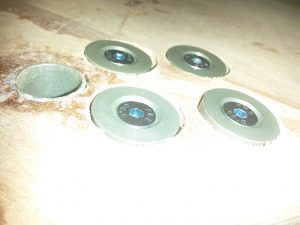
Probesitz Hülsen.
Das Einharzen der Hülsen und der Buchenwinkel war eine längere Sache, da man die Schrauben, Dämpfer und den Fahrwerksbolzen zum Verspannen während des Verklebens braucht, diese aber keine bleibende Verbindung mit den Hülsen eingehen sollen. Mal gespannt, wie das nach dem Aushärten wieder auseinandergeht…
Edit 28.05.: Schrauben ließen sich ohne Widerwillen wieder entfernen. Hülsen bündig an C3 verschliffen und damit die (ersten) 1.000 Baustunden geknackt.