Zunächst Fahrwerksschwinge entformt, was ein größerer Act war. Die Schwinge wiegt vor der Besäumung glatt 6 kg, was eigentlich ~0,5 kg zu wenig ist; bedeutet: zu viel Harz drin (da die Dichte von Glasfaser 2,6 g/cm³ und von Harz 1,15 g/cm³ ist). Es gibt aber auch eine Tabelle, die spricht von 5,2 kg. <Ironie>So ein Glück, dass die Unterlagen wohlgeordnet und widerspruchsfrei sind</Ironie>.
Die Schwinge wird später einem Belastungstest unterzogen, bevor sie fertig eingebaut wird. Ich traue dem Braten nicht (gerade, weil der Konstrukteur darauf hinweist, dass bereits 3 von 9 Selberbauern ihre Schwinge neu machen)…
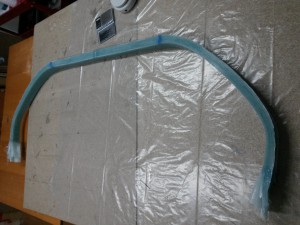
Fahrwerksschwinge vor dem Besäumen.
… und dann kamen die restlichen Formteile an die Reihe. Alles schön nass-in-nass laminiert:
- Tanks: Die Gaz’aile2 verfügt über mehrere Rumpftanks. Der eine sitzt vor/unter den Sitzen, der andere hinter dem Instrumentenbrett „auf den Knien“. Ich bin mir noch nicht sicher, ob ich den Zusatztank genau so einsetzen werde, wie von den Formen vorgegeben (Position gefällt mir nicht, ist der Avionik etwas im Weg). Alle Tanks sind aus 106 g/m² Glasfaser, 170 g/m² Aramid. Gewicht Haupttank: 535 g. Tanksumpf: 41 g. Zusatztank: 683 g.
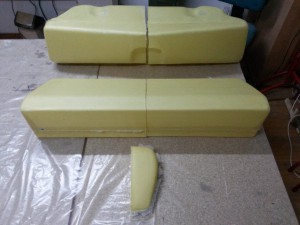
V. o. n. u.: Zusatztank, Haupttank, Tanksumpf.
- Kühlluft-Einlass: 106 g/m² Glasfaser, 170 g/m² Aramid = 253 g.
- Kühlluft-Auslass: 106 g/m² Glasfaser, 170 g/m² Aramid = 149 g.
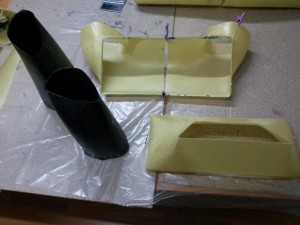
Kühlluftein- und -Auslässe.
- Verlängerungen Kühllufteinlass: 106 g/m² Glasfaser, 196 g/m² Carbon = 271 g (beide zusammen). Die werden später teilweise an die Motorhaube, teilweise in das Brandschott eingeklebt.
- Radschuhe Hauptfahrwerk: Die sind etwas komplizierter im Aufbau: 106 g/m² Glasfaser, 170 g/m² Aramid. Die Verstärkungen habe ich statt aus Aramid aus 210 g/cm² Aramid/Carbon-Hybridgewebe hergestellt. Gewicht: 289/293 g.
- Radschuh Bugrad: 106 g/m² Glasfaser, 210 g/m² Kohle/Aramid Hybrid, Loch innen mit 300 g/m² Glas überdeckt. Verkleidung Bugradstrebe: 106 g/m² Glasfaser, 170 g/m² Aramid = 92 g (da wird noch einiges abgeschnitten).
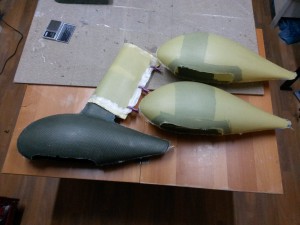
Bugradverkleidung, Hauptradschuhe.
- Verkleidung Seitenleitwerk: 106 g/m² Glasfaser, 170 g/m² Aramid = 79 g.
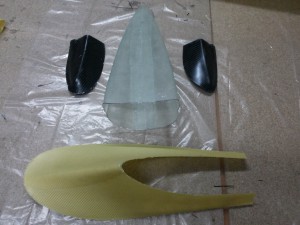
Rumpfspitze, Übergänge Rumpf-HLW/SLW.
- L-Winkel, mit denen später die Motorhauben am Brandschott befestigt werden: 106 g/m² Glasfaser, 2x 196 g/m² Carbon = 143 g. Die 300 g/m² Glas-Decklage ergänze ich später.
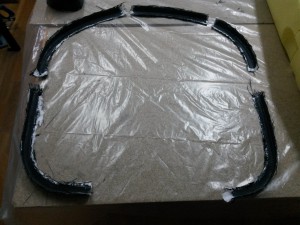
Winkel Motorhaubenbefestigung.
Weiterhin war noch eine Form für den Motor-Lufteinlass da, aber der hat die glatte Seite außen statt innen. Das werde ich später nur als Urmodell missbrauchen (muss sowieso mit Temperaturbeständigem Harz gebaut werden, das habe ich aber nicht da):
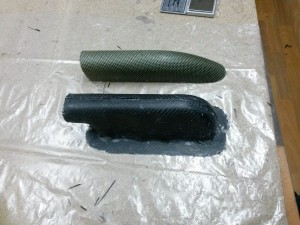
Auspuffverkleidung, Motor-Lufteinlass (grobform).
Noch etwas zum Gewicht: Insgesamt sind meine Formteile zusammen ca. 1,1 kg schwerer geworden als die angegebene Referenz (bei dieser gibt es aber einen erheblichen Anteil Luft zwischen den Gewebelagen, das wollte ich zugunsten der Bauteilfestigkeit nicht riskieren). Ist auch der Technik geschuldet (alles Handlaminat). Das von mir zuerst angedachte Vakuumpressen habe ich aufgrund der Kosten (Lochfolie, Saugflies, …), zur Verfügung stehende Zeit und Wabbeligkeit der Formen nicht realisiert.
Resumee: Alles in allem war das Abformen eine Aktion von ganzen 4 Wochen, hat mich ~7 kg Harz gekostet und um einige Erfahrungen reicher gemacht (wie immer). Manche „Schönheit“ ist der knapp bemessenen Zeit zum Opfer gefallen (habe die Ausleihzeit gut ausgenutzt…). Wird beim Finish nachher seine Zeit kosten, das wieder zu richten.