Die Gazaile verfügt original über zwei AFK-Rumpftanks mit zusammen 60 l Kapazität („auf dem Schoß“ hinter dem Armaturenbrett und unter den Knien). Kann man prinzipiell machen, aber es gibt gleich mehrere Argumente dagegen:
- Epoxidharz ist (auch mit diversen Beschichtungen aus anderen Harzen) nicht besonders kraftstoffbeständig. Es gibt daher leider mehr als genug Experimentals und UL’s, deren GFK-Tanks nach wenigen Jahren „sifften“ oder sich das Harz aufgelöst und Kraftstofffilter verstopft hat. Ersteres ist bei einer Holz-Tragfläche, nun ja, ungünstig. Zweites ist nur dann unschön, wenn man mal wieder langsam und niedrig (z.B. beim Start) und/oder kein begeisterter Segelflieger ist ;-).
- Im Falle eines Crashs werden die Tanks gerne vom zurückdrängenden Motor aufgerissen, der Kraftstoff fließt einem über die Beine und entzündet sich am heißen Auspuff…
- Last, but not least: Die Tragflächenwurzel / der Holm wird mehr belastet als mit Flächentanks.
Daher bekommen unsere (Mario und meine) Gazaile’s Alu-Flächentanks. Einmal dicht, immer dicht. Den unvermeidbaren Gewichtsnachteil ggü. der AFK-Lösung (ca. 4 kg für alle Tanks zusammen) nehmen wir dafür gerne in Kauf.
Dazu habe ich eine von innen in die D-förmige Torsionsnase der Tragfläche einschiebbare Tankform entworfen. Die Nasen-Halbrippen werden ausgehöhlt und mit CFK verstärkt (deren Festigkeit habe ich vorher berechnet). Da Aluminium im Gegensatz zu GFK/AFK nicht besonders flexibel ist, bekommt jede Tragfläche aufgrund der Verformung bei hoher g-Belastung zwei miteinander verbundene Einzeltanks.
Erste „Anprobe“ der gelaserten und gekanteten Teile aus 1 mm AW6082-Blech (hier der Innentank):
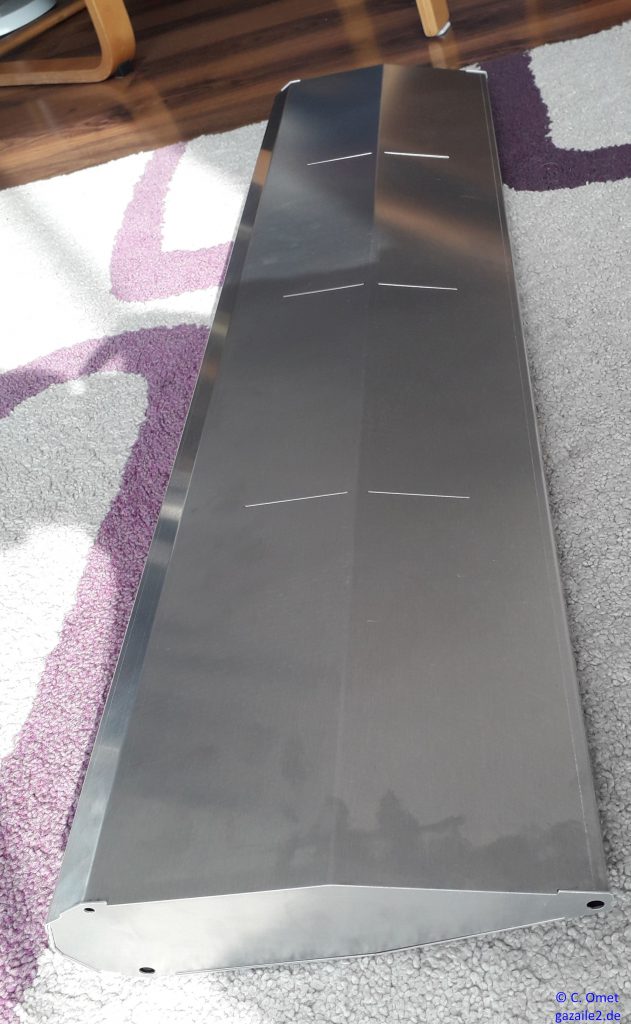
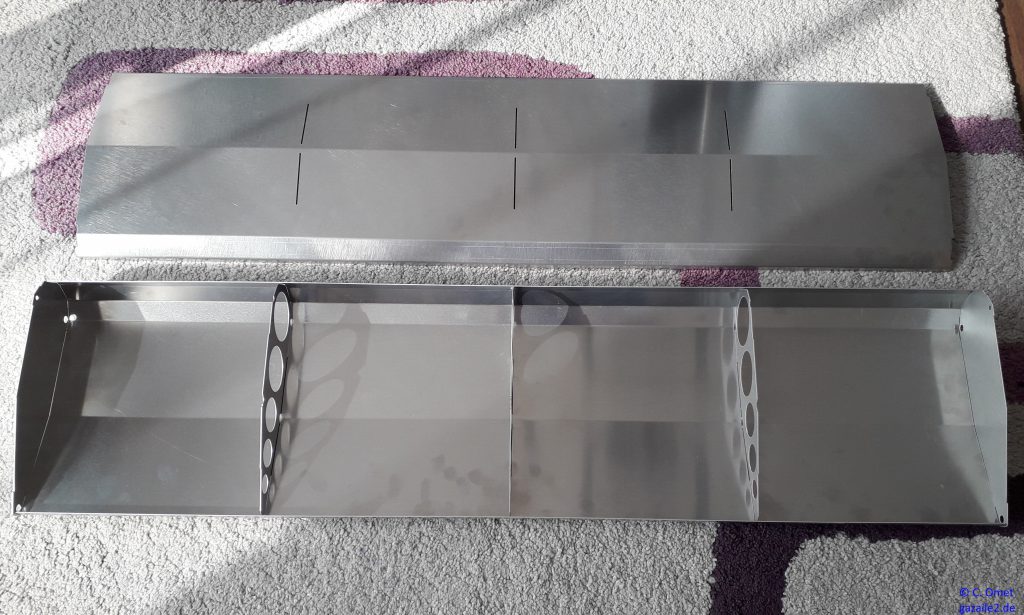
Dazu gibt’s für die Kraftstoffentnahme auch die passenden Schlauchnippel mit Schweißende (aus dem gleichen Material – da lohnt sich mal wieder meine auf CNC umgebaute Drehbank 🙂 ):
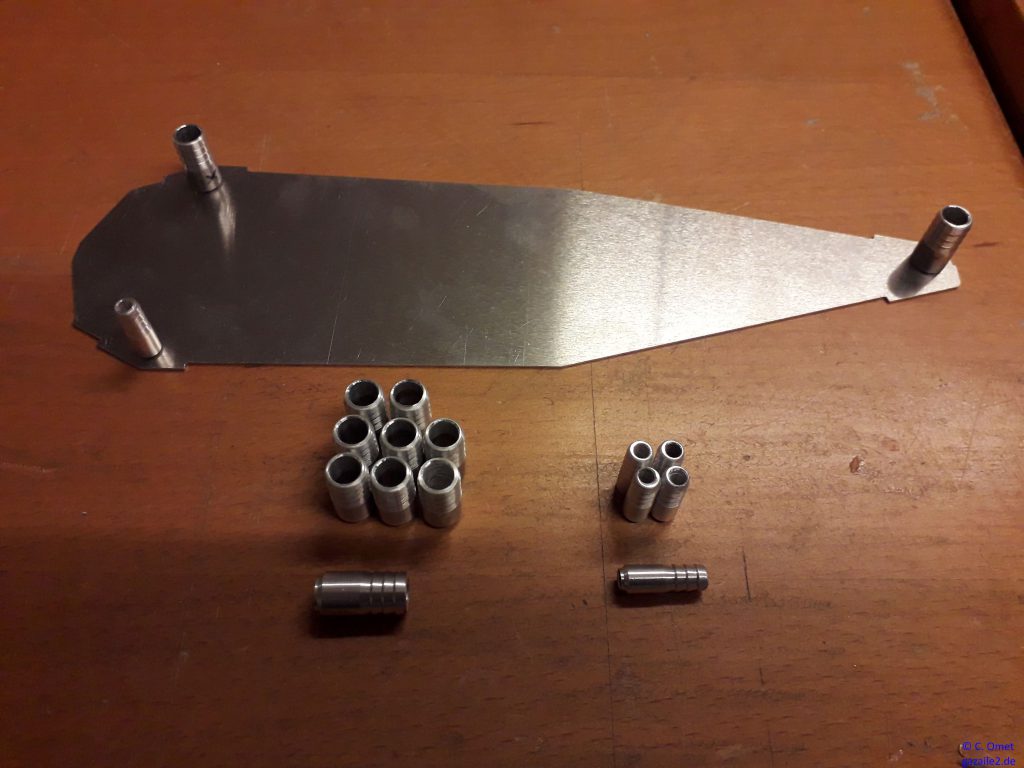
Ob die Rohrquerschnitte und Wandstärken/Verstärkungsrippen alle richtig berechnet sind, wird die erste Probebetankung mit Wasser nach dem Verschweißen zeigen. Fortsetzung folgt (Schweißen, dann Drucktest – vielleicht können die Tanks noch ein wenig leichter werden).
Bei Interesse: Die Tanks kann man von uns „beziehen“…