Es gibt natürlich immer wieder Arbeiten für den Flieger, die trotzdem keinen Fortschritt direkt am Flieger bedeuten: Dazu zählt bei mir die Vorbereitung der „großen“ Werkstatt:
Alle fahrbaren Untersätze aus der Garage verbannt. Was dazu nötig war: Grassoden neben der Gartenhütte abgetragen (was für eine Plackerei), 5,5 m² Gehwegplatten in zwei Fuhren vom Baumarkt geholt (eine ging nicht, das Auto musste auch so schon genug leiden):
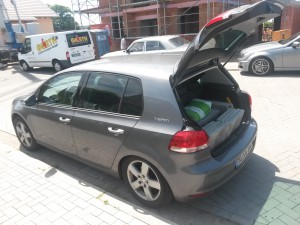
Golf – konkret tiefergelegt!
… und verlegt. Bodenanker in Beton eingegossen, Ständerbauwerk aus Holz errichtet, Nut+Feder-Dach darüber (hält mich und meinen jüngsten aus), Dachpappe draufgenagelt und das Holz lasiert. Fahrradständer druntergestellt und dann endlich Fahrräder aus der Garage verbannt.
Der Garagentorantrieb hat eine veränderte Hebelmechanik bekommen und schließt nun endlich nahtlos am Boden ab; damit kommt auch hier jetzt kein Regenwasser mehr rein. Der Weg von der Garagentür zur Haus-Hintertür wurde gepflastert, so dass der Weg von der Kellerwerkstatt zur Garagenwerkstatt sauber begehbar ist.
Alles zusammen hat mich insgesamt fast zwei Wochen Planung und Durchführung gekostet.
Damit ist nun alles vorbereitet zum Aufbau des Rumpfes 🙂 pardon der Rumpfhelling, denn die will auch noch gebaut werden… ach so, und meine D14 H7-Reibahle ist auch gekommen!