Heute waren mal wieder ein paar Drehteile dran. Mario hat dankenswerterweise das Verbindungsrohr für die Klappen besorgt, so dass ich nun die Teile an die Rohrmaße anpassen konnte.
Die zwei Anschläge habe ich aus AW7075 gedreht. Sie wiegen jeweils nur 6 g dank der vielen Ø7-Löcher. Das FEM sagt, bei 100 N Last verbiegen die sich um ganze 0,5 µm. Ich denke, das ist OK. Jeweils 3,5 g pro Stück gespart.
Die drei Rohrschellen mit der CNC-Fräse direkt aus AW7075 ausgefräst (1x programmieren, 3x abfahren 🙂 ). Die entstandene Passung auf dem Rohr mit 0,05 mm Spiel genügt, die Teile werde ich später zusätzlich zu den Nieten mit Metallkleber fixieren.
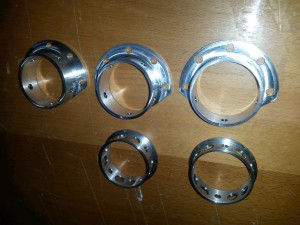
Anschläge (unten) und Rohrschellen mit Flansch für Klappen-Verbindungsrohr.
Das einzige, was etwas mühsam war: Die Verwendung des 80 mm-Teilapparats von Wabeco; der hat eine unbeschreiblich tolle (China-)Qualität:
- Schneckengetriebe hemmt an 5 Positionen, hat ansonsten zu viel Spiel (lässt sich auch nach Anleitung nicht besser justieren).
- Rundlaufgenauigkeit ist nur mit viel Mühe besser als 1/10 mm einzustellen.
- Axiales Spiel lässt sich nicht besser als 2/10 mm einstellen, ansonsten klemmt das besagte Schneckengetriebe.
- Verwendet man die Klemmschraube, dann drückt die den ganzen Flansch seitlich weg.
Ich glaube, ich schicke das Teil auf Garantie zurück. Das ist dem Werker da drüben wohl mal runtergefallen. =8-/