Der „sparsame“ Anlenkungsring für das Bugrad funktioniert nur in der endgültigen Position, da hierfür die Bugradstrebe durchbohrt werden muss. Für das Einstellen der korrekten Länge also einen weiteren Ring mit Klemmfunktion hergestellt.
Um die Länge der Bugradstrebe und des Seilzugs für dessen Federung festzulegen, muss das Bugrad belastet werden – und das am Besten mit der Originallast… daher die noch überlange Bugradstrebe eingefädelt und den Motor ans C0 montiert.
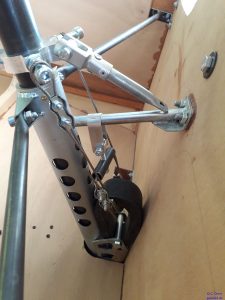
Federung entspannt.
Dann die Federelemente so lange mit einer Hilfsvorrichtung gespannt, bis das Motorgewicht das Bugrad nur noch wenig einfedern lässt. Dabei kommt der Anlenkungsring ca. 1 cm über dem Halterrohr (im Bild verzinkt) zu liegen.
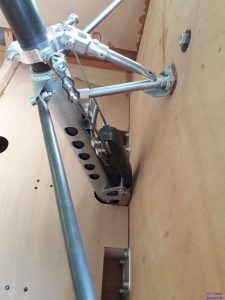
Federung gespannt!
Bei horizontaler Lage des Hauptholms befindet sich dessen Oberkante bei meinem Fahrwerk 93,5 cm über dem Boden. Damit das Ganze ohne komplette Last auf dem Hauptfahrwerk (Tragflächen, Tanks, Passagiere, Kontrollsystem, Avionik,…) halbwegs richtig ist, mussten einige Wasserkästen und Baugewichte herhalten:
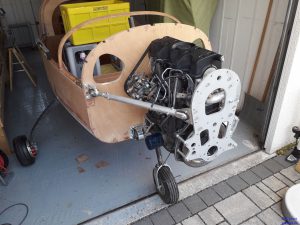
Längen korrekt eingestellt.
Die Bugradstrebe habe ich noch ca. 8 mm länger als notwendig gelassen . Man weiß nie, was bis zur Fertigstellung des Fliegers noch passiert…
Des weiteren habe ich bei der Gelegenheit den neuen Zahnriemen am Motor aufgelegt. Dann kam der spannende Moment: Ob sich er Motor frei durchdrehen lässt? Das geht, mit ordentlicher Kompression kurz vor den Totpunkten der Zylinder! 🙂
Damit kann ich endlich mit allem, was sich oberhalb der Bugradstrebe befindet, weitermachen (Seilzüge, Kühler, Verstrebungen, …) .