Länger kein Beitrag im Blog mehr, aber dafür jetzt den ganzen Fortschritt hier zusammengefasst:
Zunächst die Endleisten fürs HLW aus Oregon Pine keilförmig zugeschliffen (lustige Arbeit, da diese Leistchen wirklich sehr dünn und damit zerbrechlich sind).
Dann Holm, Rippen, vordere und hintere Halbrippen, Carbon Hinges und Abschlussleiste für Trimmklappe mit angedicktem Harz auf die obere Beplankung geklebt und fixiert. Anschließend Endrippen und Endleisten aufgeklebt und die komplette Innenseite mit verdünntem Harz versiegelt:
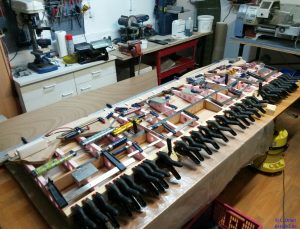
Verkleben HLW-Oberseite.
Alle Schraubenlöcher zur Befestigung der Beschläge innen mit Harz versiegelt. Dann die Beschläge in angedicktes Harz gesetzt, die Muttern mit Drehomoment angezogen und mit rotem Lackstift markiert (das ist ab jetzt meine Markierung für fix und fertige Verschraubungen):
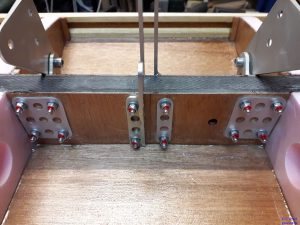
Beschläge gesetzt und gesichert.
Haltepunkt: Abnahme des Leitwerks beim Prüfer in diesem Zustand (nebst diversen anderen Teilen). Keine Beanstandungen!
Dann die untere Beplankung des HLW’s mit den, für die Beschläge notwendigen Aussparungen versehen und mit reichlich angedicktem Harz verklebt (vorher Innenseite mittels Roller zügig mit verdünntem Harz versiegelt).
Tip: Hier bietet es sich an, zwei Tische zu verwenden, die man einfach auseinanderschiebt, damit die Beschläge in der Mitte genügend Platz haben und man nicht unten drunter krabbeln muss.
Die Endleiste hat in der Mitte der Trimmklappe eine leichte Ausbuchtung bekommen; diese Stelle ist beim Verkleben der Beplankung nicht ausreichend unterstützt worden. Da werde ich wohl noch ein paar Mal mit dem Heißluftfön ran müssen…
Nach dem Trocknen die Nasenleiste an die Sollkontur angepasst (mit Hobel und Feile) und verschliffen. Mein Theophysik-Prof. hätte gesagt: „Längere, aber einfache Arbeit“. Zudem riecht frisches Apachi nach Banane… Dann die Randbögen aus Roofmate mit der passenden Aussenkontur versehen und verklebt. Nach dem Abschleifen der Randbögen diese mit 147 g/m² Glasfasergewebe (Köper) belegt, verschliffen und Ober-, Unterseite und beide Randbögen des HLW’s mit 80 g/m² Glasfasergewebe (Leinwand) belegt.
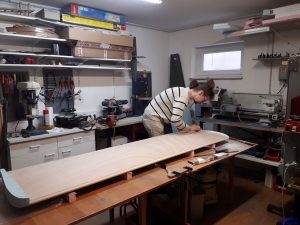
Verschleifen der Randbögen.
Schlußendlich alle Überlappungen der Glasfaser sauber verschliffen und die Trimmklappe ausgeschnitten – so vorsichtig, dass das aus Kevlar bestehende Scharnier nicht beschädigt wird. Das hat überraschenderweise sehr gut geklappt.
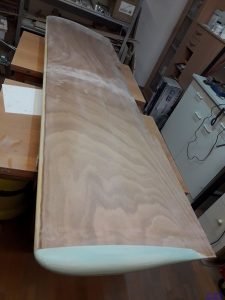
Fertig!
Nächste Etappe für dieses Bauteil: Anpassen an die Rumpfkontur (vorne mittig ausschneiden).