Die Holme mussten noch in Kohlefaser eingewickelt werden:
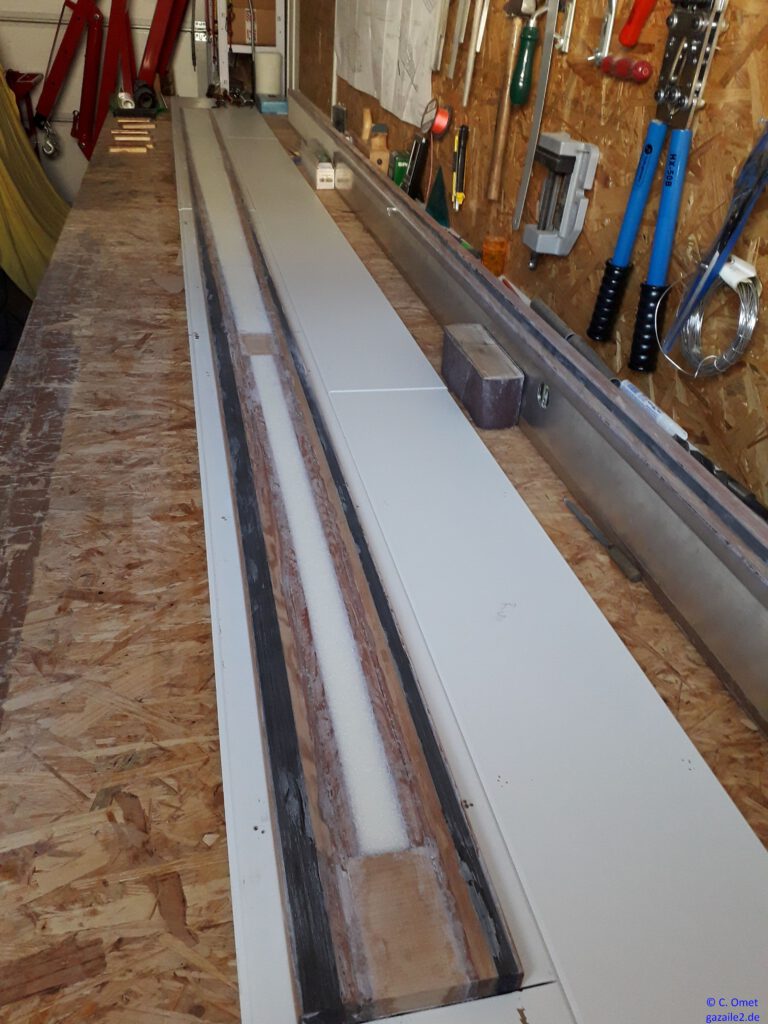
Die Holmstege bestehen aus 45° 400 g/m² Kohlefaser-Diagonalgelege. Diese werden (bis zu 3-lagig im Innenbereich) im Vakuumpressverfahren nass-in-nass aufgebracht (jeweils eine Seite zu einer Zeit)
Hierzu zunächst die Helling vorbereitet, um 1° Verwindung zwischen Flächenwurzel und -Spitze einzustellen:
Danach die Holme sauber abgeschliffen, die Holzteile wie immer mit einem leicht stumpfen Sägeblatt angeritzt. Anschließend mit Harz bepinselt, mit dem o.g. Kohlefasergelege belegt und satt mit Harz getränkt – überschüssiges Harz wurde nach der Durchtränkung mit dem Spatel wieder abgezogen. Zu guter Letzt das Abreißgewebe und Saugvlies darüber gelegt (im Innenbereich dürfen es ruhig zwei Lagen sein) und in schließlich in Folie eingesackt.
Das ganze zunächst 24 h bei Unterdruck aushärten gelassen:
Danach den Holm entformt, besäumt und beschriftet. Das Beschriften ist wichtig, da die oberen und unteren Holmgurte nicht symmetrisch sind; zudem gibt es aufgrund der Verwindung nun einen linken und einen rechten Holm.
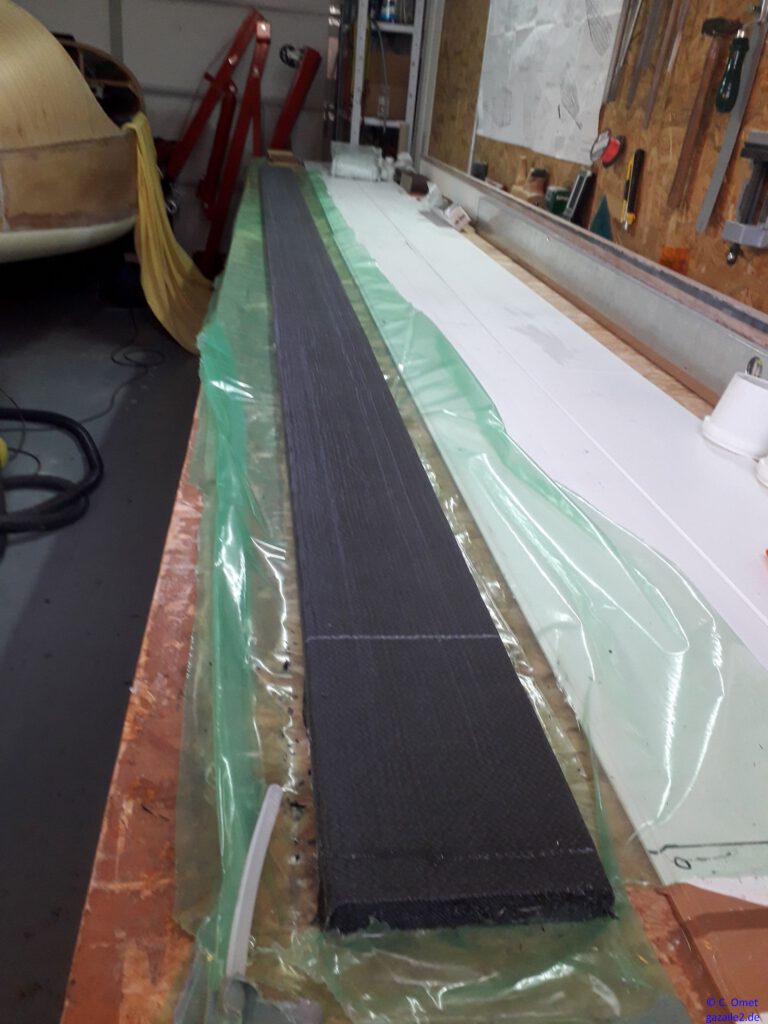
Anschließend wird das ganze Prozedere mit der Gegenseite des gleichen Holms und mit dem anderen Holm wiederholt.
Was jetzt noch aussteht, ist das Einbringen der Hauptbolzen-Buchsen. Um die einzupassen, muss der Rumpf zunächst aus der Garage raus (Garagenbreite << Spannweite!) und das Wetter dazu passen…
Danach folgt dann die Temperung der kompletten Holme.