Der 1. Versuch, geschweißte Flächentanks herzustellen, ist grandios gescheitert. Die sind krumm und schief geworden – der Schweißer hat wohl noch nie dünnes Alu geschweißt. Aber das ist ja nicht das erste Mal, das etwas schiefgeht…
Also neuer Versuch mit kpl. anderer Konstruktion, diesmal aus gelasertem AW 6061, genietet und mit Dichtmasse. Das ganze Konstrukt ist 1,4 m lang und fasst pro Seite ca. 22 l. Die vier Baffles sollen den Tankinhalt am im Schiebezustand am herumschwappen hindern und werden mit Becherblindnieten befestigt. Die Füllstandmessung erfolgt über kapazitive Geber (ähnlich der RV-7).
Erste Unterseite mit Hilfe des Sohnemanns, etlichen Clecos und Blechklemmen passgenau gebohrt (sorry, das Bild ist etwas unscharf):
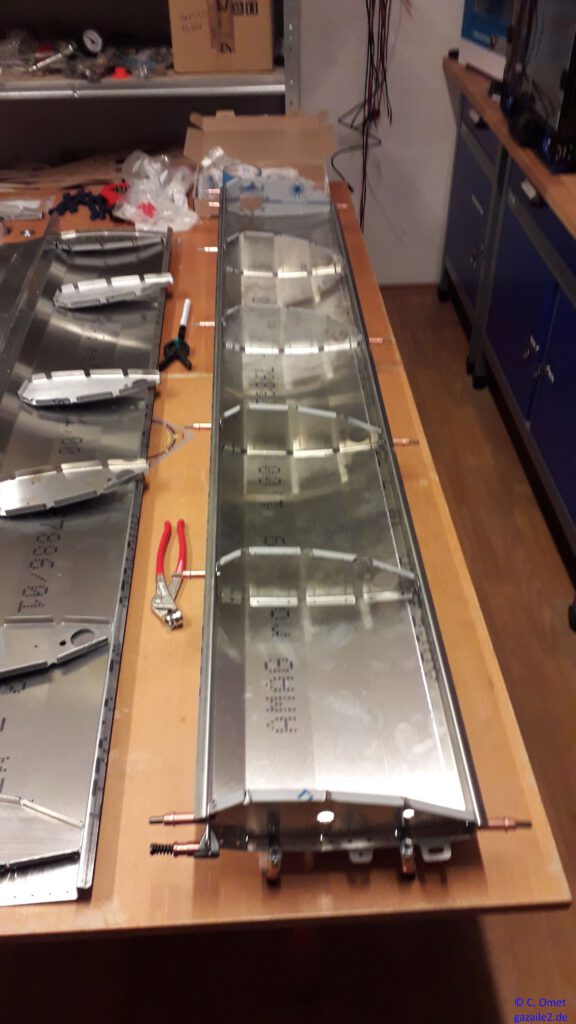
… und: Nein, man kann nicht genug Clecos haben (gleich welche nachbestellt).